Stand-up pouches: a guide for beginners and advanced users


All components of a stand-up pouch
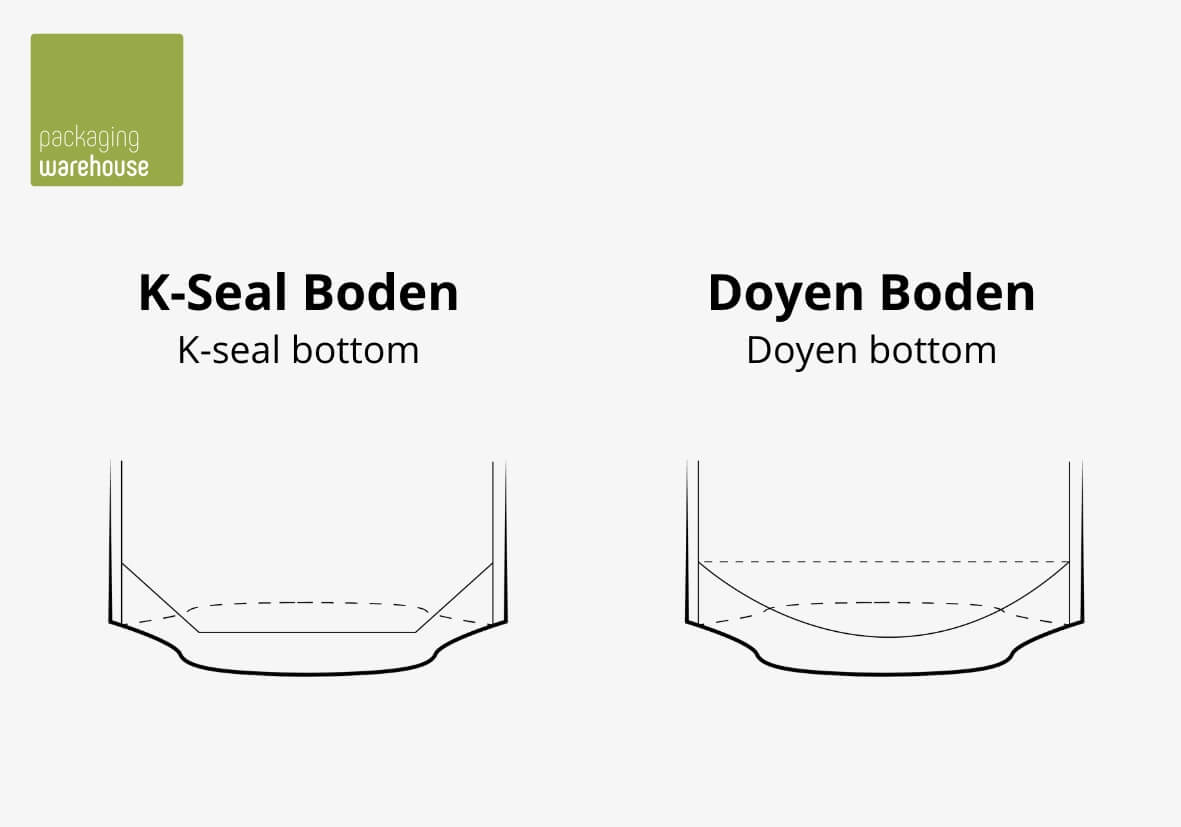
Stand-up pouches can be produced in many different ways. There are different production techniques, especially regarding the bottom fold. A difference is made above all between a normal Doyen bottom and a so-called K-seal bottom.
The two variants differ in the way the bottom fold of the pouch is integrated between the front and the back. The Doyen bottom has the disadvantage that a format-specific tool has to be ordered for it in each case. The K-seal bottom, on the other hand, has the advantage that any format can be produced with one and the same tool.
Plastic or paper stand-up pouches
A stand-up pouch can be made from a wide variety of materials. The most common material combinations are:
- Composite plastics such as PET/PE
- Kraft papers such as KRAFT/PET/PP
Depending on the material, different properties result in terms of feel, print image, food compatibility and recycling. Especially pouches made of kraft paper are very popular, provide a very high-quality feel and always convey a sustainable image. In most cases, however, the material combinations of paper and plastic used are not officially recyclable (in Germany).
In order to be able to recycle a stand-up pouch, the material used must be made of a so-called mono-material (e.g. PE/EVOH/PE). It is important that both the foil and components such as the zipper are made of one and the same material (PE foil + PE zipper). The most common mono materials are made of mono-PE and mono-PP.
Plastic-free or industrially compostable stand-up pouches are also available, but these do not meet the same high requirements for the necessary barrier functions as, for example, an EVOH barrier does. The inner coatings of these pouches often consist of ultra-thin varnishes or organic coatings. These pouches usually also have significantly lower stability and durability.
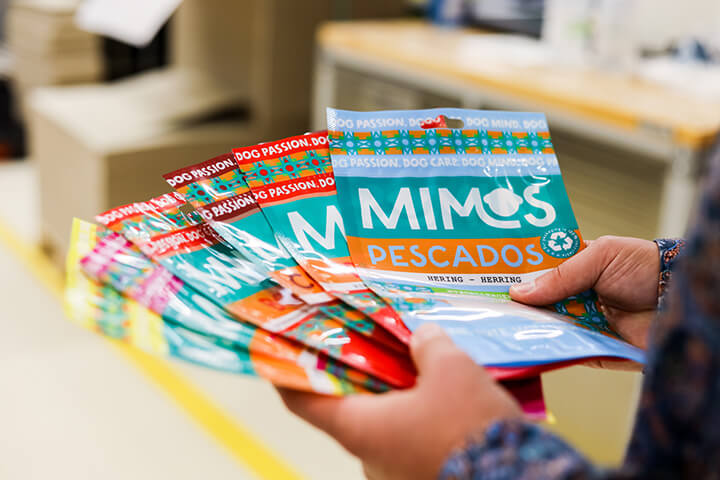
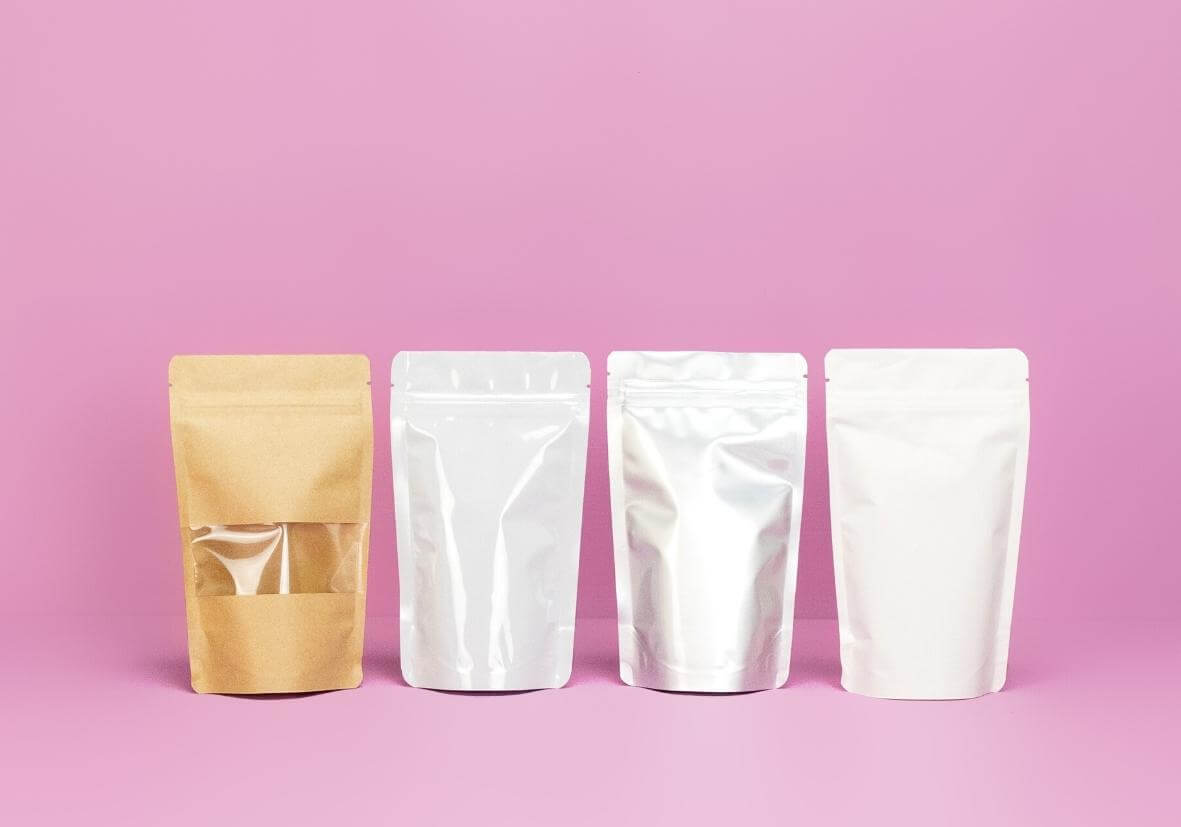
Our range of materials
Our range includes a wide range of materials for stand-up pouches and flat pouches. Here you are guaranteed to find the right material for every requirement:
Recyclable mono-plastics:
- PE/EVOH/PE in white (Full-PE)
- PE/EVOH/PE in transparent (Full-PE)
Composite Plastics:
- PET/EVOH/PE in white
- PET/EVOH/PE in transparent
- metPET/EVOH/PE in silver metallic
Kraft paper materials:
- Kraft paper brown / EVOH/PE
- Kraft paper white / EVOH/PE
All our mono- and composite plastics are optionally available with a glossy or matt surface.
The components of a stand-up pouch
Depending on the application, a stand-up pouch can be equipped with a wide variety of components. For the right component selection, you should ask yourself a few questions beforehand:
- Will the pouch be standing or hanging at the POS?
- Will the pouch be resealed after it has been opened for the first time?
- Must the contents of the pouch be visible at the POS?
- Is the pouch a refill?
- Are aromatic products such as coffee or tea filled?
Based on these questions, you can find out whether you need the following components or not:
- Euro slot hanger to hang the pouch on the POS.
- Zipper to reseal the pouch.
- Viewing window for a first impression of the contents.
- Spout for refilling containers (spout bag / spout pouch).
- Aroma valve to protect the aroma of coffee or tea.
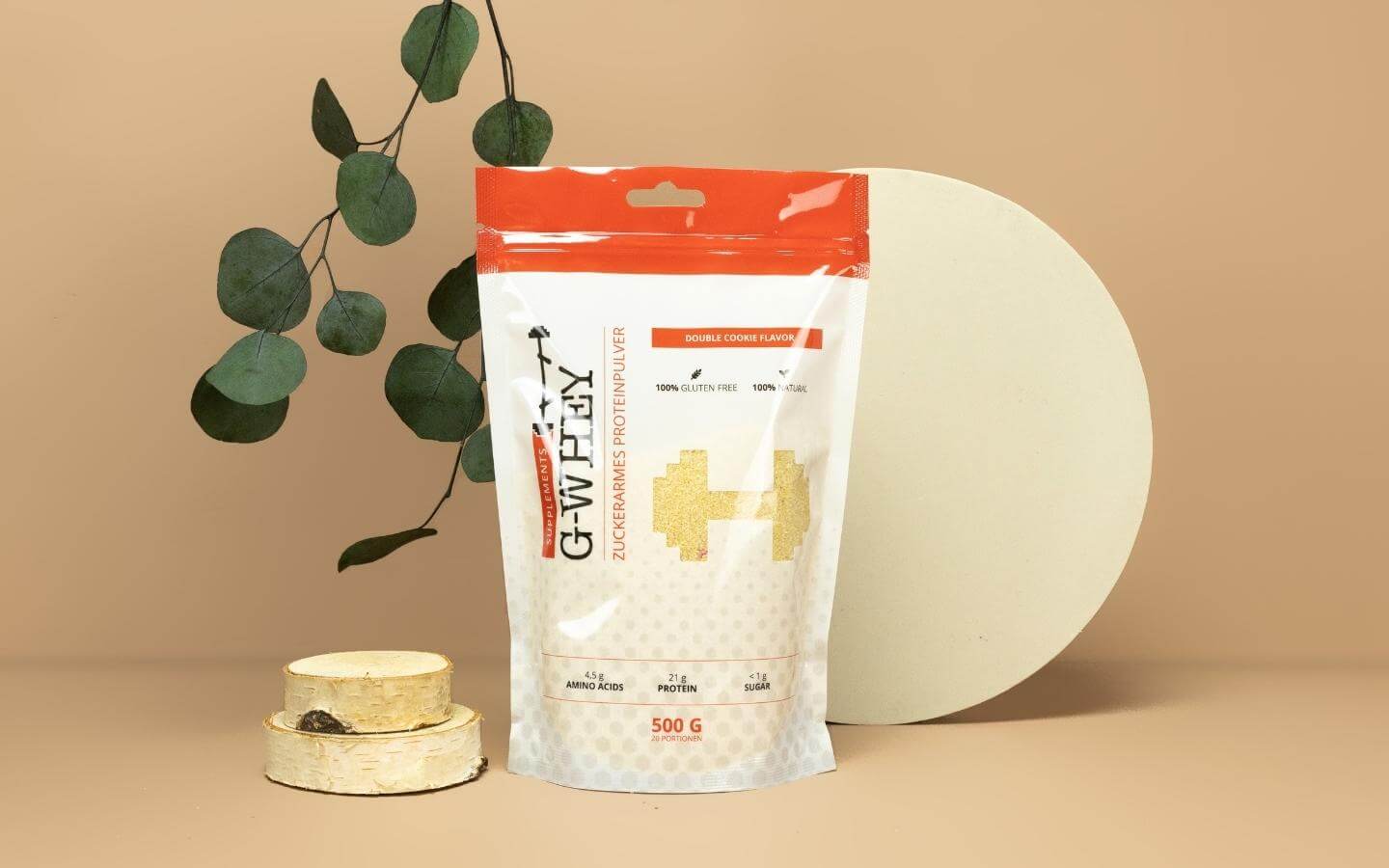
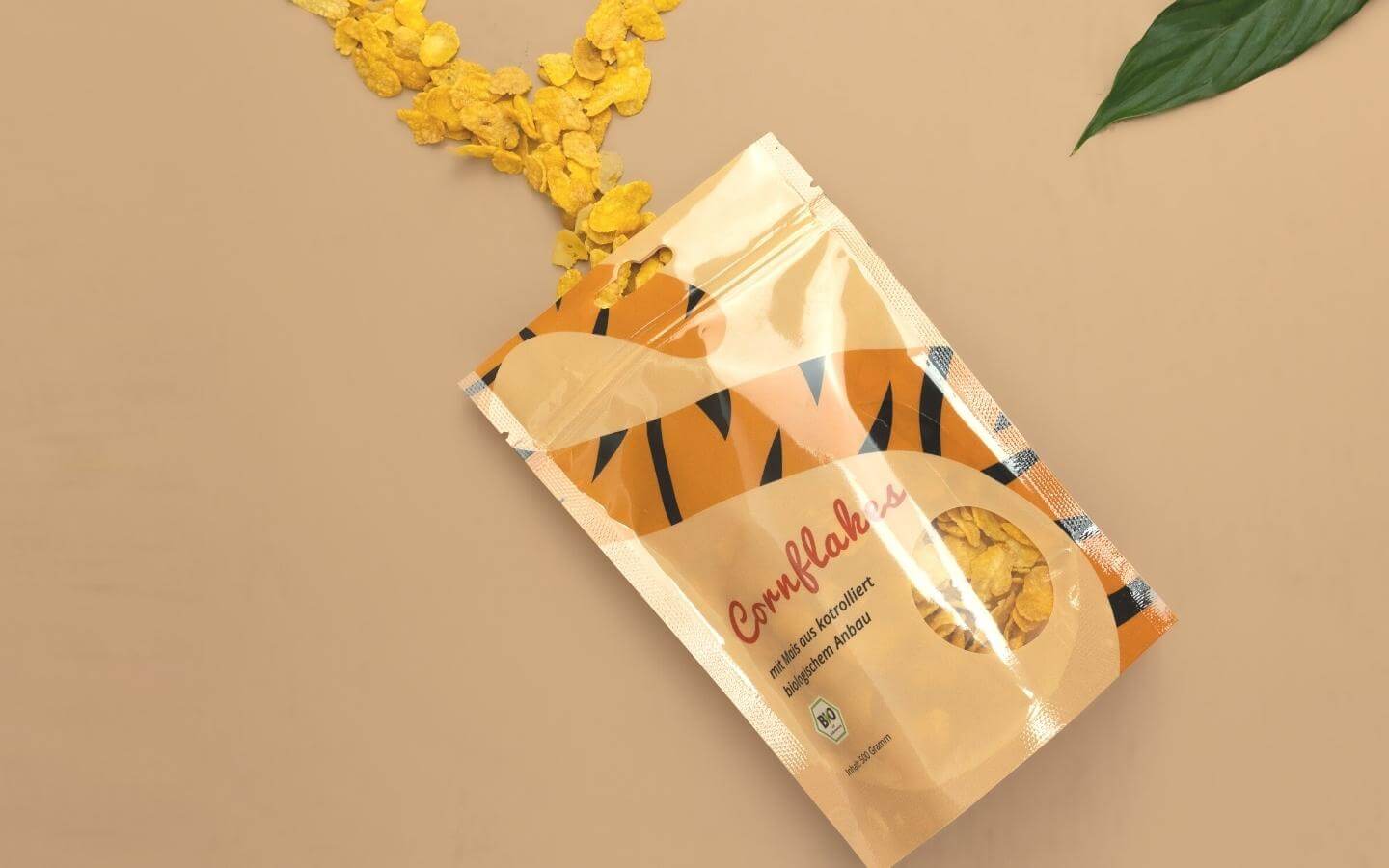
Stand up pouch with viewing window
Pouches with a viewing window are particularly suitable for optimum presentation of goods at the point of sale. The viewing window is highly transparent, can be specified in variable size and all barrier properties of the material are of course still fully retained.rlich weiterhin voll erhalten.
For an individual viewing window, it is necessary to select a transparent foil. This foil is the requirement for transparent / see-through areas. A viewing window is automatically created in all areas that are not printed. However, so that the printed areas of the pouch do not also appear slightly transparent, an additional opaque ink is often printed under the printed image. We use a so-called opaque white for this, which ensures that the background of the printed areas is no longer transparent. For this option, you can select in our calculator the color "4-color Euroscale + white".
You can find out how these requirements must be technically implemented in the print data in our print data instructions for stand-up pouches.
Unique metallic effects
In order to be able to implement more eye-catching packaging designs, we also offer our standard pouch foil in a silver metallic version. The surface of the foil is double-sided metallic and allows special metallic effects. The resulting effect is comparable to hot foil stamping. The advantage, however, is that any desired color can be metallized. The structure of the print data is very similar to the structure of the stand-up pouches with viewing window.
All printed areas that are not backed with opaque white (HPI-White) automatically appear metallic. All elements with opaque white background (images, texts, shapes, etc.) have no metallic effect.
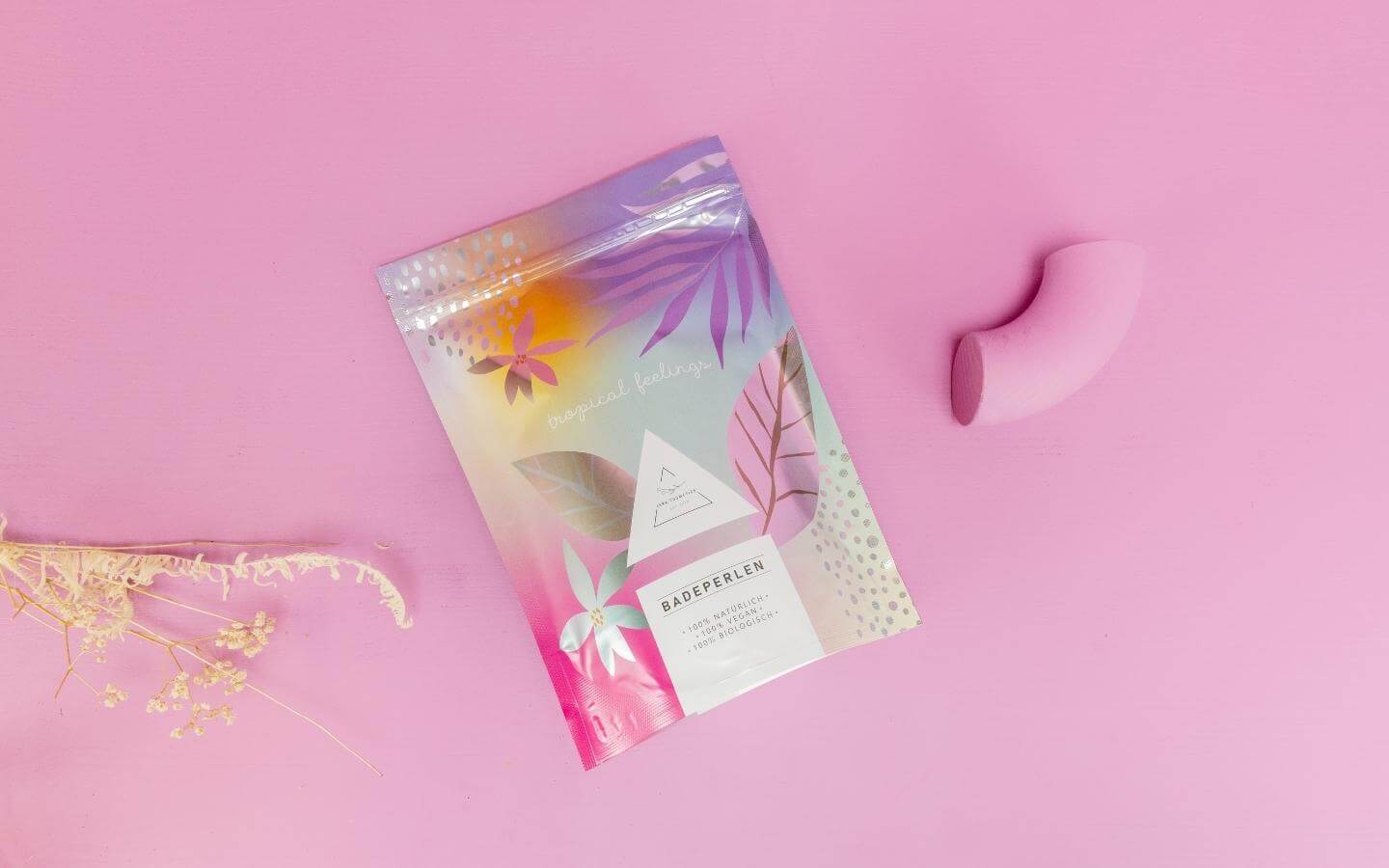
Stand up pouches individual printing
The production of stand-up pouches
.jpg)
The printing process
Stand-up pouches are basically printed from roll to roll. This means that an unprinted roll of material is clamped at the front end of the machine, printed during the process and rewound as a roll at the rear end.
Stand-up pouches made of foil consist of two individual foils, one of which is printed in the printing process (print foil 12 and 25 µm thick). The second, unprinted foil layer is then added subsequently in the laminating process. The advantage is that the print image is then enclosed between two layers of material. This protects the print from external influences and scratches.
Stand-up pouches made of paper also consist of two individual components. On the inside the barrier foil, on the outside the kraft paper (brown or white). In the printing process, this material is already in its final composition on the roll and the paper surface is printed directly. The printer ink can optimally adhere to the rough surface of the untreated paper.
The lamination of the foils
Lamination is also known as the marriage of the two foils and is the key process for more complex material combinations. During the process, the very thin printing foil and the thicker laminating foil are brought together at high speed. A food-safe special adhesive ensures perfect adhesion of the foils. A lot of experience is required here, because the result depends heavily on the speed, adhesive thickness and web tension. Errors can lead to wrinkling or other material defects.
As an alternative to the lamination process with an adhesive, lamination with heat is also possible - also called thermo-lamination. Thermo-lamination is particularly suitable for stand-up pouches whose contents have to be treated with heat after filling (autoclave/autoclave).
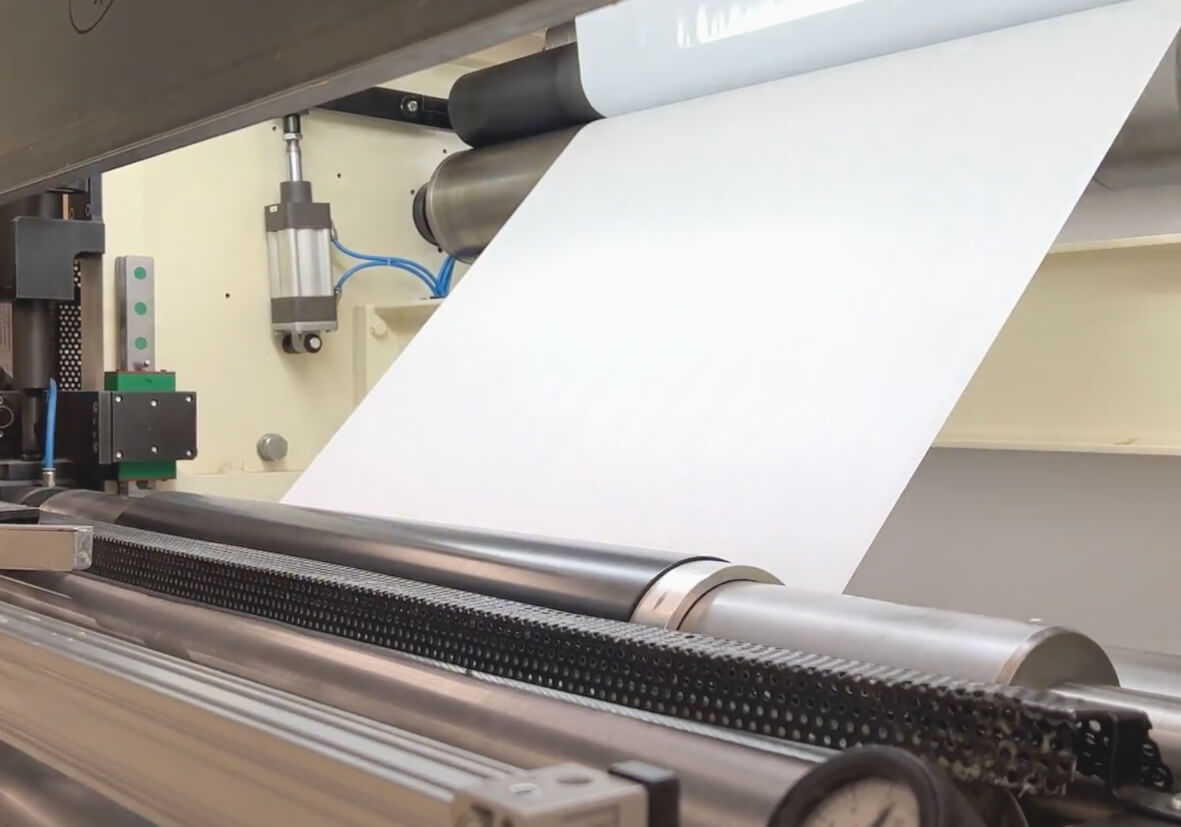
The production of stand-up pouches
After the printing and laminating process is complete, the finished roll is waiting for further processing on the Doypack machine. This machine has the following tasks:
- The merging of the front, the back and the bottom of the pouch.
- The insertion of the zipper.
- The welding of the edges and the bottom fold.
- The punching of the Euro hole and the tear off tabs.
- Separating the individual pouches from the web.
High safety due to safe barriers
Because most stand-up pouches are intended for direct contact with food or pet food, the pouch materials must meet many different requirements. The main concern is the protection and durability of the contents. The contents must be protected from the following influences:
- UV radiation
- Humidity / water vapor
- Oxygen
Depending on the contents, the flexible packaging market uses either materials with no barrier, materials with a low barrier, or materials with a very high barrier. The barrier layers used for this purpose are divided into organic and inorganic barriers. Each barrier must be of sufficient thickness to ensure adequate protection for the contents.
- Inorganic barriers: e.g. aluminum foils, silicon oxide (SiOx), etc.
- Organic barriers: e.g. polyamide (PA), ethylene vinyl alcohol (EVOH), etc.
The industry standard barrier film thicknesses are between 2-8 µm. The EVOH barrier is one of the most effective barriers against oxygen, aromas and water vapor.
.jpg)