Part 1: Customized folding boxes - Which box for my product?
.jpg)

YOUR WAY TO THE PERFECT FOLDING BOX
Folding boxes are simple constructions. Nevertheless, there are some important factors to consider when choosing the type of box and the detailed configuration. Therefore, before you get started, you should determine exactly what requirements your packaging must meet. To do this, it is useful to find answers to the following questions:
- How big and heavy is the product?
- Does the product have sharp edges or pointed prongs?
- Is the product fragile or otherwise sensitive?
- What is the transport route and how long does it take?
- What external influences does the product need protection from?
The answers to these questions provide a good indication of what the optimum packaging for your product might look like. In the first part of our guide, we show you which box types, materials and box bases are basically suitable for your product.
THE SELECTION OF THE BOX TYPE
Today folding boxes come in various designs and shapes. So it doesn't always have to be a standard model - certainly not if you want the product to stand out from the competition. Here are a few examples from our range:
- Pillow boxes stand out mainly due to their shapely pillow silhouette, thanks to which they look particularly elegant and playful. Pillow boxes are particularly popular, for example, as packaging for soaps, scarves, glasses, jewelry and sweets.
- Counter displays are packaging and sales presentation at the same time. In this way, you can place larger quantities of your product in just one box and prepare it perfectly for presentation at the point of sale with creative designs.
- Flat cardboard sleeves are the packaging for super-slim content. A typical example is the use as a noble protective cover for vouchers, tickets and membership cards.
- folding boxes with hinged lid are a particularly classy variant of the folding box and can be used for a wide range of products. Thanks to the hinged lid with two tuck-in flaps on the sides, these boxes can be resealed very easily and reliably.
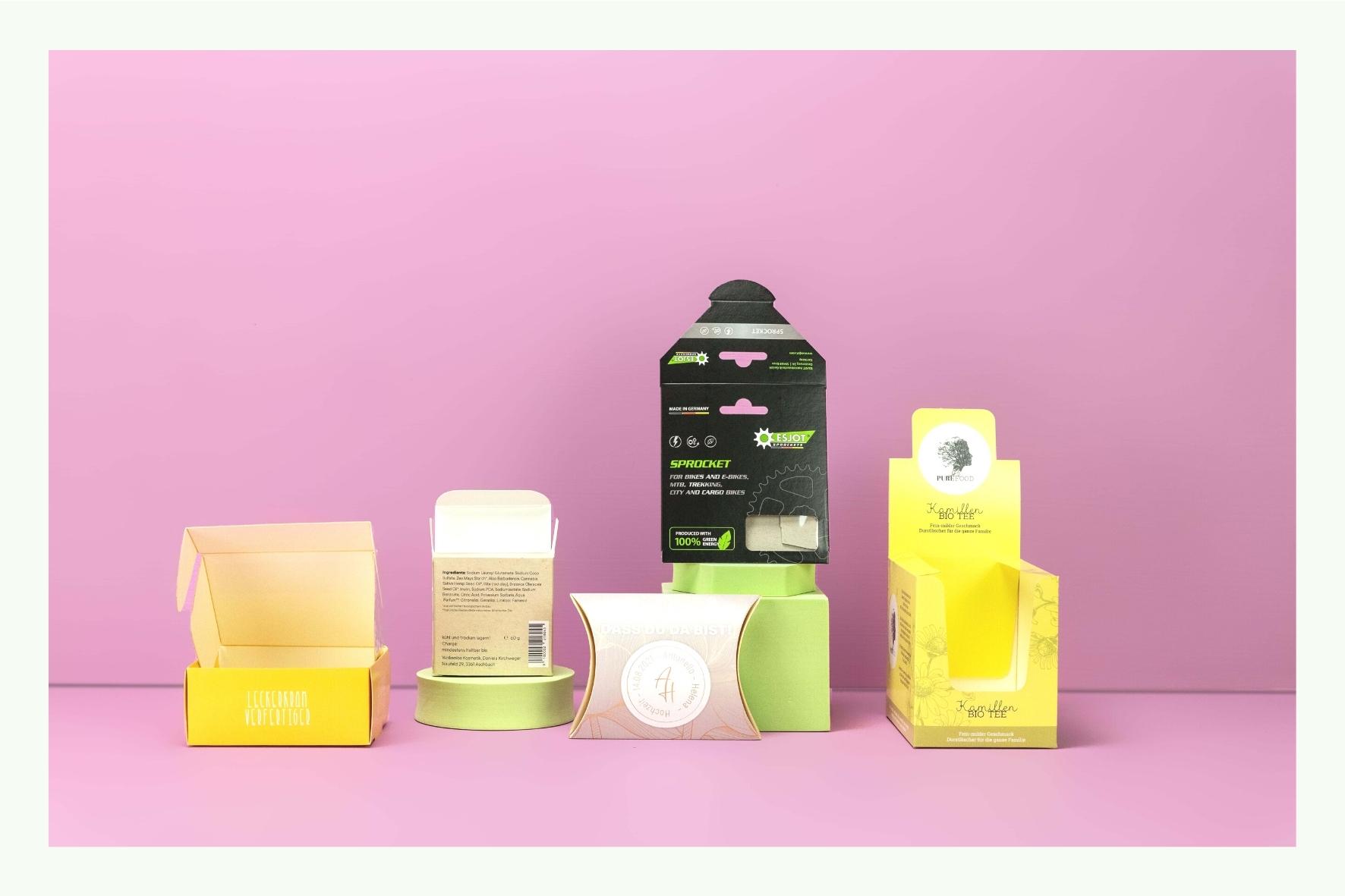
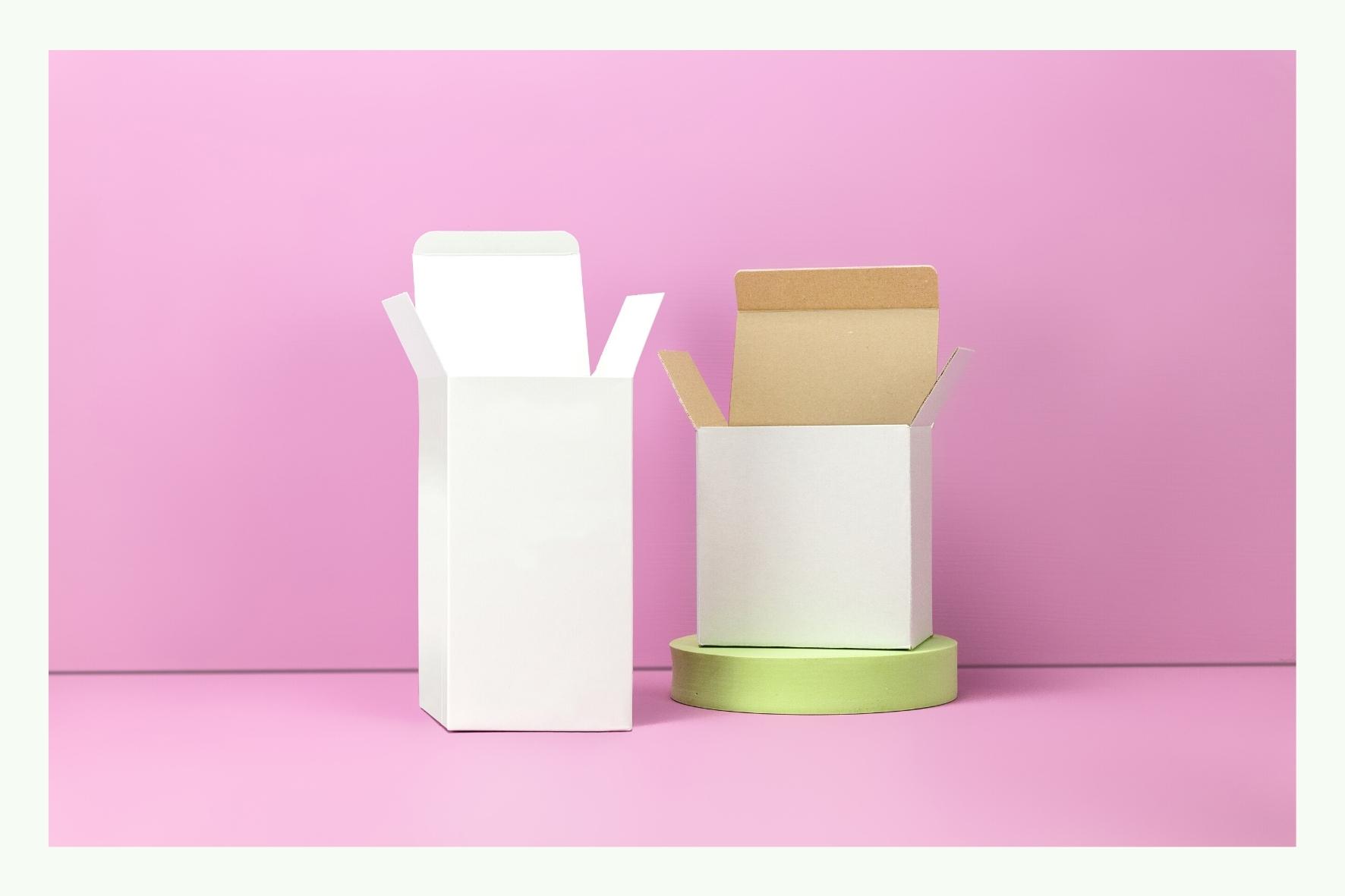
CARDBOARD OR CORRUGATED BOARD?
The material is a decisive factor for the load capacity of your folding box. Although the terms cardboard and corrugated board are often used synonymously in everyday life, there are significant differences:
- Cardboard is made from vegetable fibers and is basically nothing more than thick paper with a grammage of 150 to 600 g/m2 - the higher the grammage, the more robust the cardboard. Folding cartons made of cardboard offer excellent protection for many goods, such as cosmetics and foodstuffs - and are also the more economical and ecologically beneficial choice of material.
- Corrugated board consists of several paper layers: the paper flute and the flat paper sheets glued to it. The load capacity largely depends on the type of flute used: for example, the W flute is more robust than the finer E flute.
- Folding boxes made of corrugated board are more robust and have a higher load capacity than their cardboard counterparts and therefore offer optimum protective properties for particularly large, heavy and sensitive products. They are also suitable, for example, as e-commerce packaging for shipping.
FINDING THE RIGHT BASE
Regardless of whether you want folding boxes made of cardboard or corrugated board, you can choose between different base types for some box types. The three variants differ in their construction and therefore also in their load capacity and robustness.
1. Folding boxes with tuck-in flaps are the simplest and most cost-effective option. The base and lid are identical and each consists of two dust flaps and a tuck-in flap for closing. This type is particularly suitable for light goods.
2. Folding boxes with snap lock base are slightly more robust, as their base flaps interlock when they are closed. This provides additional stability. Snap lock bases are primarily used for light and medium-weight products.
3. Folding boxes with crash lock base are the most robust variant. This is ensured by the glued flaps, which close automatically when the box is put in place. Crash lock bases therefore provide a secure hold even for medium-weight and heavy products.
1. Folding boxes with tuck-in flaps are the simplest and most cost-effective option. The base and lid are identical and each consists of two dust flaps and a tuck-in flap for closing. This type is particularly suitable for light goods.
2. Folding boxes with snap lock base are slightly more robust, as their base flaps interlock when they are closed. This provides additional stability. Snap lock bases are primarily used for light and medium-weight products.
3. Folding boxes with crash lock base are the most robust variant. This is ensured by the glued flaps, which close automatically when the box is put in place. Crash lock bases therefore provide a secure hold even for medium-weight and heavy products.
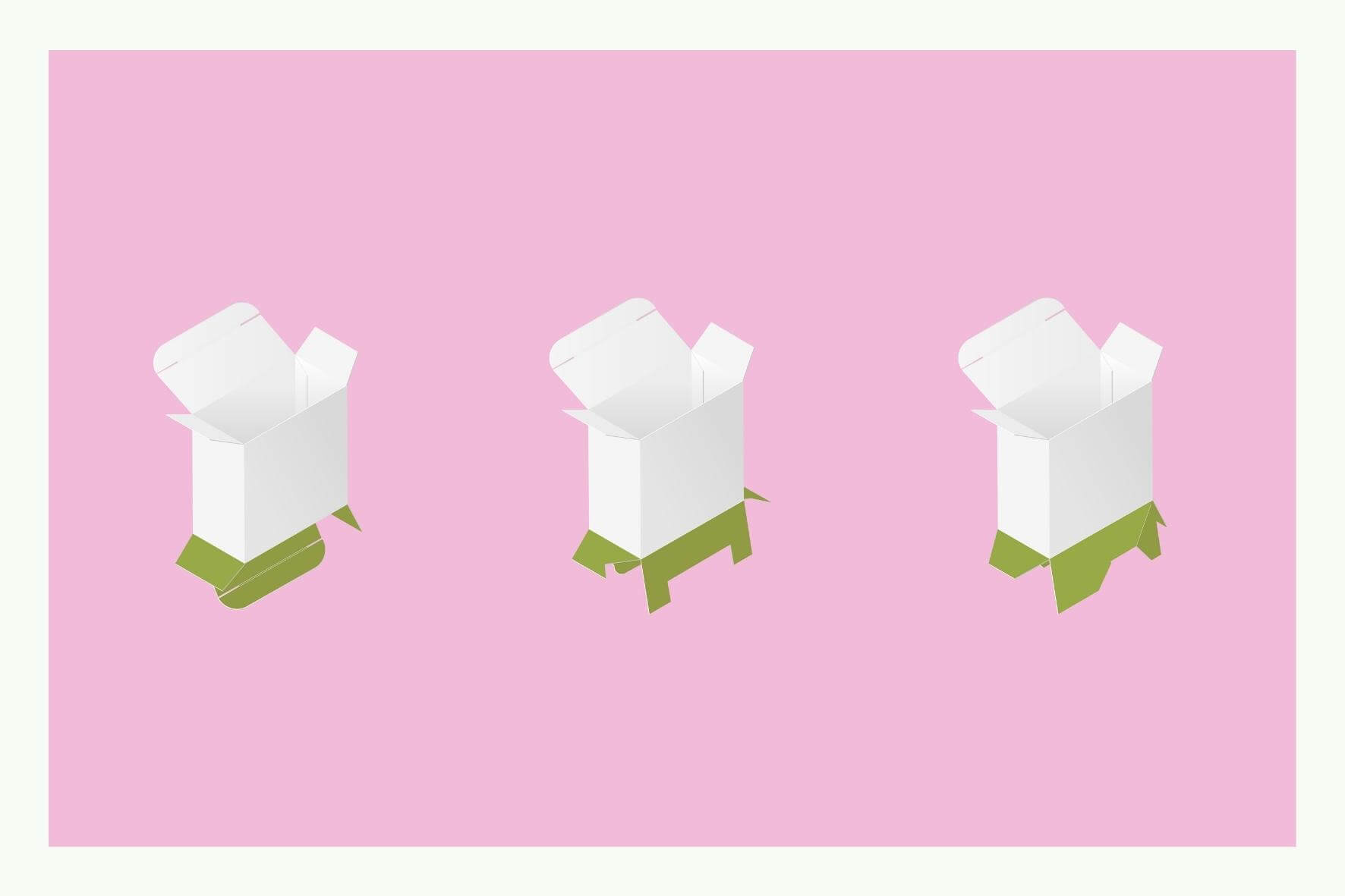
Reading recommendation: Continue in part 2 of our guide. There we look at the box format, the possible protective coatings and other optional configurations.